Joining medical applications quickly and sustainably with ultrasonics
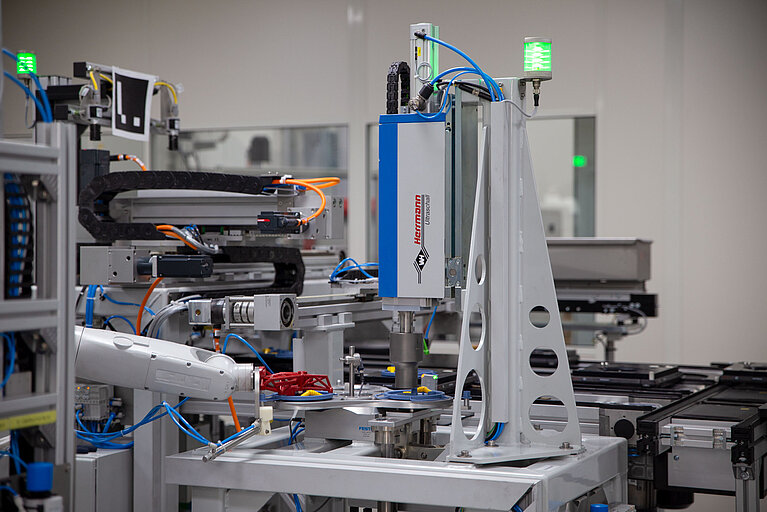
Connecting medical plastics without adhesives
Connecting plastics without adhesives: Using ultrasonics as a joining technology, companies can produce their applications skin-friendly and eco-friendly. If certain specifications for the components are met, the process can also be used for sensitive applications with complex geometries.
To produce medical applications more sustainably and at the same time more cost-effectively, companies shift their increasingly to the joining process. It offers great potential for increasing cycle rates or product quality, but must meet the high demands on the sometimes sensitive components.
Ultrasonic welding is one of the joining processes that has been tried and tested in the medical industry for years. It is used for the manufacturing of a wide range of applications, such as dialysis filters, infusion pipes or infusion sets and pumps for diabetes patients.
Minimal stress on the components
In ultrasonic welding, plastic parts are connected using friction with minimal force. To do this, an ultrasonic generator creates a frequency of between 20 and 35 kHz, which is converted into mechanical vibrations by a converter.
These vibrations are transferred to one of the two joining partners via the welding tool - the sonotrode. Friction occurs at contact points between the two components that have been defined beforehand. During the short welding time of a few hundredths of a second, heat is generated at these points and the plastic melts.
The big advantage: this melt creates high-strength and dense connections at a molecular level. This protects the inside of the applications from contamination and other external environmental influences.
The components themselves remain virtually free from thermal or mechanical loads, making ultrasonic welding suitable for particularly sensitive devices and contents.
Skin-friendly and sustainable
Such connections without additional joining agents are also advantageous for applications that are worn directly on the body, such as blood glucose meters or insulin pumps. The adhesives containing isobornyl acrylate (IBOA) that are still frequently used in these applications can limit wearing comfort or even lead to skin irritation. Without the chemicals in the adhesives, skin tolerance improves enormously.
The product's environmental balance sheet also benefits from the adhesive-free process. In addition to the use of additional joining agents, energy-intensive processes such as heating or cooling the adhesive are also eliminated. This means that energy is only used where it is actually needed: at the weld seam of the components.
Precise control using parameters
The energy input can be precisely controlled during the process, as can the other welding parameters, which were determined beforehand in laboratory tests.
Central parameters for the welding of plastics are above all:
- Frequency
- Amplitude
- Welding force
- Energy
- Welding path and velocity
These parameters influence each other. The accurate definition of the correct welding parameters is therefore one of the most important steps in the development of the ultrasonics welding process. Once they have been found, they can be reliably reproduced. This ensures consistent, safe welding results.
Digital quality control
As the welding tools make direct contact with the plastic components during the process, this contact can be used to collect valuable feedback in the form of data. The most important data can be visualized in graphs so that the welding process can be evaluated immediately.
A total of up to 150 dates per weld can be measured, saved and evaluated. This information not only makes an important contribution to quality control. It also provides decisive indications of how the process can be further optimized in order to optimize velocity, rejects and energy consumption.
High potential for automation
Due to the accuracy of the control options and the short process cycles, ultrasonics is often used in the medical sector in particular where high quantities need to be produced with consistent results. Depending on the application, the welding process takes between 80 and 500 ms. Smaller medical applications in particular, such as connectors for infusion sets, often only require around 150 ms.
It is also possible to integrate individual ultrasonic components on collaborative robots or multi-head machines. For smaller quantities that also need to be manufactured reliably and with consistent quality, manual work stations can be used.
Conditions for welding with ultrasonics
To benefit from the advantages of ultrasonic welding, the components must be designed accordingly. Almost all thermoplastic materials can be connected with ultrasonics. This also includes the most common plastics in the medical industry, such as:
- Polypropylene (PP)
- Polyethylene (PE)
- Acrylonitrile butadiene styrene (ABS)
For ultrasonic welding, components can also be filigree or designed in complex 3D shapes. Even the thinnest wall thicknesses of around 1 millimeter can be realized with this technology.
In addition, the components require a special joint design at the contact point of the joining partners. A so-called energy director can be used to ensure that the plastic only melts at the desired point.
The right joint design for the component and the customer's requirements is another decisive success factor for welding with ultrasonics. That's why it's an advantage if the ultrasonic supplier is already involved in the development of the product. With the appropriate experience, they can consult on both the choice of material and the design of the component. This saves valuable time in product development and thus ensures a competitive advantage.
The biggest advantages of ultrasonic welding:
- Real-time process data monitoring
- Helps to achieve sustainability goals
- High process stability
- Low reject rates
- Very suitable for high production volumes
Frequent use cases of ultrasonic welding in medical applications:
- Welding of injection-molded parts
- Connection of films and membranes with plastic housings
- Manufacture of certain functional properties
- Welding of nonwoven materials and band-aids to a housing
- Beading a septum under pre-tension