Automated connection of medical components for maximum output
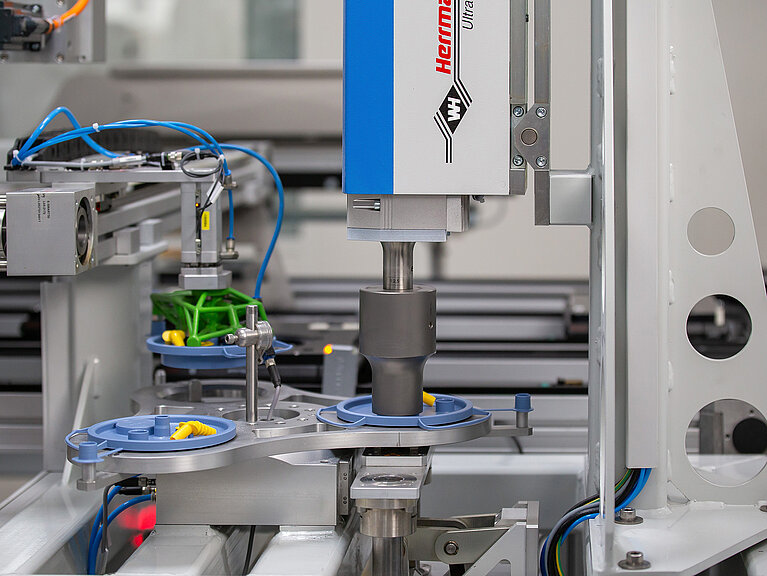
Increasing Output with Ultrasonics as a Joining Technology
Perfect for automated assembly: Thanks to minimized welding times and real-time process control, ultrasonics is ideal for manufacturing medical components in high volumes. Find out the advantages of the technology for your application in this article.
To save costs and minimize possible rejects, numerous products and components are manufactured through automation, especially in the medical industry. However, to ensure that consistent, perfect connections are created even at high cycle rates, manufacturers need the right joining process.
Ultrasonics offers several advantages for the automated manufacturing of medical products such as CGMs, infusion sets, and insulin pumps.
The biggest advantages for companies are:
- Minimal welding times
- Evaluable digital process control
- Simple integration
- High OEE (overall equipment effectiveness)
- Traceability
Minimal Welding Times for Medical Plastics:
Unlike many other common processes, ultrasonics connects plastics without additional joining agents. In this way, ultrasonic welding requires zero preheating, shortening cycle times and eliminates the need for adhesives, reducing costs. Instead, the welding tools are immediately ready and deliver consistently perfect results from the first to the last weld, even in continuous use.
The welding times themselves are extremely short. Depending on the application, ultrasonic welding takes between approx. 80 and 500 ms. Smaller medical applications in particular, such as connectors for infusion sets, usually only require around 150 ms.
Digital Process Control In Real Time:
The welding process is controlled via the generator, where the ideal parameters for the process are saved, which were individually determined for the application beforehand in tests in the ultrasonic laboratory.
In the production environment, these parameters can be reliably reproduced in each individual process. This ensures optimum process stability when creating connections, ensuring the functionality of critical applications such as insulin pumps, surgical instruments, and laboratory equipment.
Another decisive advantage: data can be collected in real time during the process. This is possible due to the direct contact between the welding tool and the component. In total, up to 150 pieces of welding data are transmitted to the generator, where they can be saved and accessed at any time.
This amount of data forms an invaluable basis for seamless quality control and trends. It can also be used for further process optimization to make manufacturing even faster, more efficient and safer.
Easy integration into new & existing systems:
Welding with ultrasonics can be used in various ways for the automated manufacturing of medical applications. The most common possible ways are:
- Integrated welding system in an automation line
- Individual components in special welding machines
- Flexible use in robot cells
Production lines can be retrofitted with ultrasonics, even if alternative joining processes are currently used.
In-depth consulting and sufficient experience are required for smooth integration of the modules or components. That is why our experts are at your side in every phase of the collaboration: from the development of the welding solution to the start-up of the systems and beyond.
Automate your manufacturing assembly processes and start your ultrasonics project with us!
Discover how ultrasonic welding can help optimize the manufacture of your medical products.