Secure and Fast Connections for Cables of all Cross-Sections
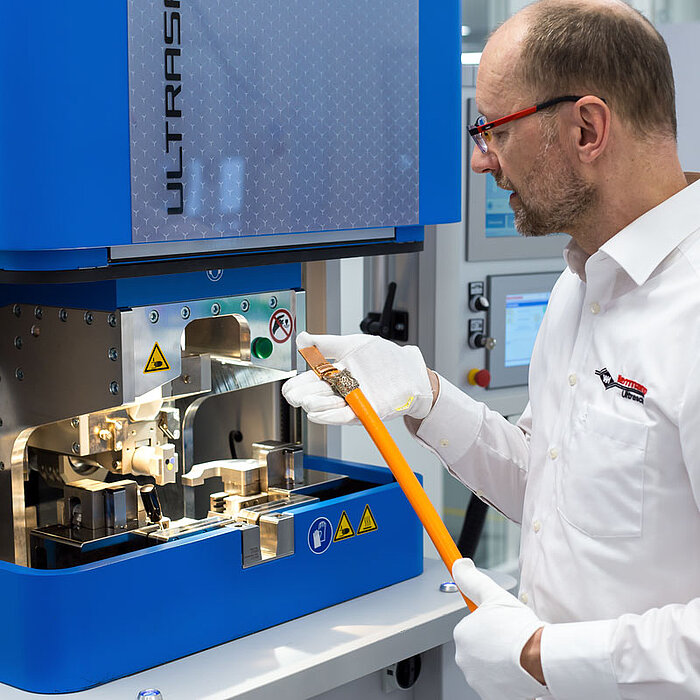
Benefit from fast production cycles of just a few seconds: With up to 12,000 W of power, you can reliably connect cables with even the largest cross-sections in the shortest possible time.
Thanks to our innovative converter architecture, you no longer need any cooling times. This ensures maximum OEE when creating strong wire-to-terminal or terminal-to-terminal connections.
Weld your cables or busbars with ultrasonics and increase your output!
Your benefits of ultrasonic welding:
- High strength
- No losses in conductivity
- Short cycle times without cooling times
- Permanent process monitoring
- Reliable and reproducible connections
White Paper: 3 Boosters for E-Mobility – download now!
From batteries and wire-to-terminal connections to plastic components: Many applications in electric vehicles benefit from ultrasonics as a joining technology.
Use the technology to permanently:
✔ Permanently reduce production costs
✔ Increase the range of the EV
✔ Make manufacturing processes more efficient & sustainable
Learn how to overcome the key challenges of e-mobility with ultrasonic welding!
Discover new solutions today
Boost Your Electrical Connections with Ultrasonic Welding
Ultrasonic welding can offer you added value at every connection where electricity flows: Busbars or High-voltage cables benefit from strong, reliable connections without contact resistance.
Discover the most common applications for ultrasonics welding and learn more about your benefits!
Download Expert Resources
Discover new ways of welding your battery or wire-terminal application and learn more about our innovative technology! Our downloads contain the knowledge from over 60 years of ultrasonics, providing valuable insights into advanced assembly techniques. By sharing our technical knowledge with you, we ensure a close partnership on equal terms so that we can realize projects as quickly and successfully as possible.
Download our exclusive resources to stay ahead of your competition.
FAQ – The Most Important Questions and Answers about Welding Metals with Ultrasonics
Ultrasonics can be used to safely connect the same and different non-ferrous metals within a very short time. It is mainly used for the connection of conductive non-ferrous and precious metals. These include aluminum, silver, copper and nickel in particular, with aluminum-copper connections accounting for 90% of applications.
Weldable non-ferrous metals are all pure metals except iron as well as alloys (connections of different metals) that have less than 50 percent iron content. Pure ferrous metals cannot be joined with ultrasonics.
Due to the optimal conductivity of the connections and the short welding times, ultrasonic welding has established itself as a joining technology for numerous applications consisting of non-ferrous metals. These typically include:
- Wire-terminal
- High-voltage cable
- Busbar / terminal terminal
- Lithium-ion battery (LIB)
- Pouch cells and flexible housings
- Battery management systems
Learn more about ultrasonic welding for your wire-terminal application.
Ultrasonic welding is a joining process without additional joining agents. Mechanical vibrations are created by an ultrasonic generator and converter. The welding tool, the so-called sonotrode, transfers these mechanical vibrations to the components.
One joining part vibrates in the longitudinal direction, while the other remains secured in the fixture. Friction breaks up the oxide layer and the parts are welded together at the same time under pressure.
The decisive factor in welding is not the heat generated, which is well below the melting point, but the relative movement of the two joining partners.
Learn more about the principle of ultrasonic welding for wire-terminal applications.
Ultrasonic welding of metals has several advantages over conventional welding methods such as soldering, crimping or laser welding:
- Speed: The welding process with ultrasonics only takes fractions of a second. Without the need for additional cooling times, production cycles can be significantly accelerated.
- Reliability: The specification and monitoring of numerous welding parameters ensures precise and reproducible welding results. This is a decisive advantage, especially when welding sensitive and small metal parts, such as in batteries.
- Cost efficiency: Ultrasonic welding does not require any additional joining materials such as solder.
- Sustainability: Ultrasonics welding requires very little energy as it does not use heat to connect metals and does not require the use of chemical tools.
- Safety: Ultrasonic welding produces no sparks or smoke, which makes it safe to work in manufacturing.
- Gentle: Materials are not damaged or deformed outside the defined weld area.
Learn more about the benefits of ultrasonic welding for your wire-terminal application.
When welding with ultrasonics, the ideal parameters are determined individually for each application via test series in the ultrasonic laboratory. These can be reproduced exactly thanks to the precise process control.
Up to 150 different welding data can be recorded, saved and exported for each individual welding process. This monitoring is fully automated and ensures seamless digital quality control.
This ensures a safe, reliable process and minimizes scrap rates – and costs – over the long term.
Learn more about the benefits of ultrasonic welding for your wire-terminal application.
Partner with Us
Contact us to discover how our premium solutions can elevate the quality and effectiveness of your large-scale production in the metal industry. We look forward to hearing from you!