How to Seal Ready Meals Safely & Reliably
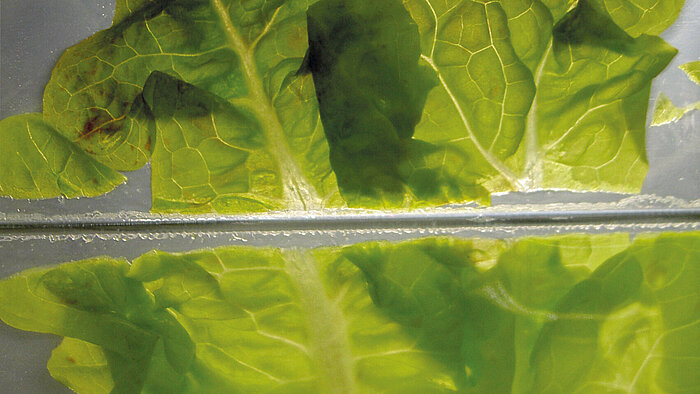
Are you also affected by reject rates as high as 6 to 14 %? Rejects often result from contamination in the sealing area or the use of unsuitable systems for increasingly demanding packaging materials.
With ultrasonic sealing, you benefit from:
- Reliable sealing through contamination
- Gentle, precise process for sustainable materials
- Automated & digital process control
Work with us to permanently increase the safety and sustainability in your packaging process.
White Paper: 5 Success Factors for Hermetic & Sustainable Seals
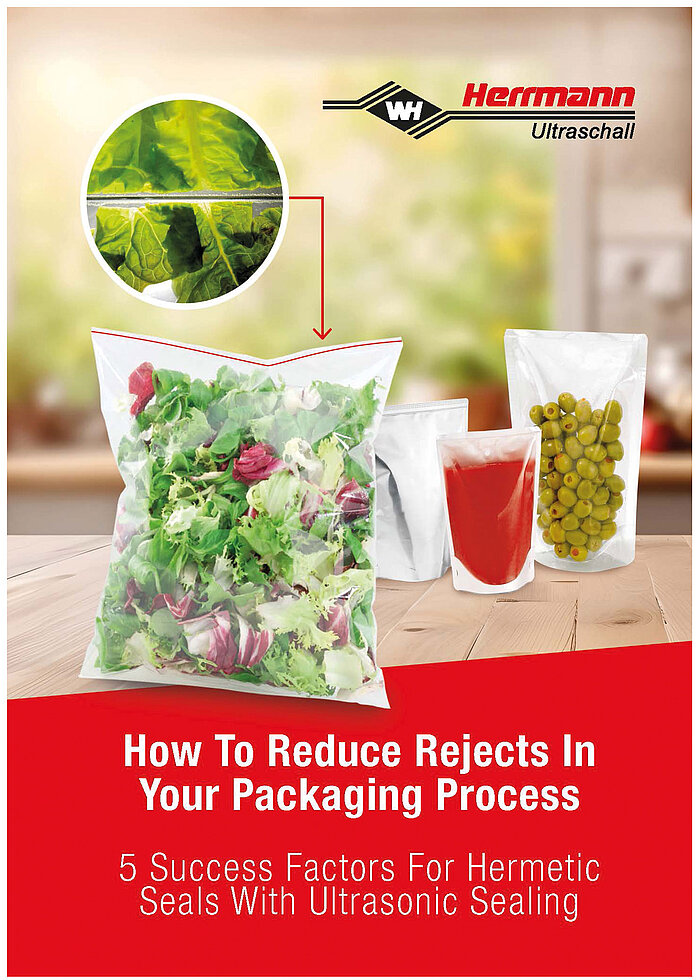
Our new white paper provides clear, practical examples to show how ultrasonics can eliminate the most common causes of rejects while also increasing the sustainability of your packaging process.
Learn how you can:
✔ Significantly reduce your waste over time
✔ Package in a PPWR-compliant and sustainable manner
✔ Implement automated quality control options
Unlock 60+ years of our know-how today
Frequently solved packaging applications for Ready Meals
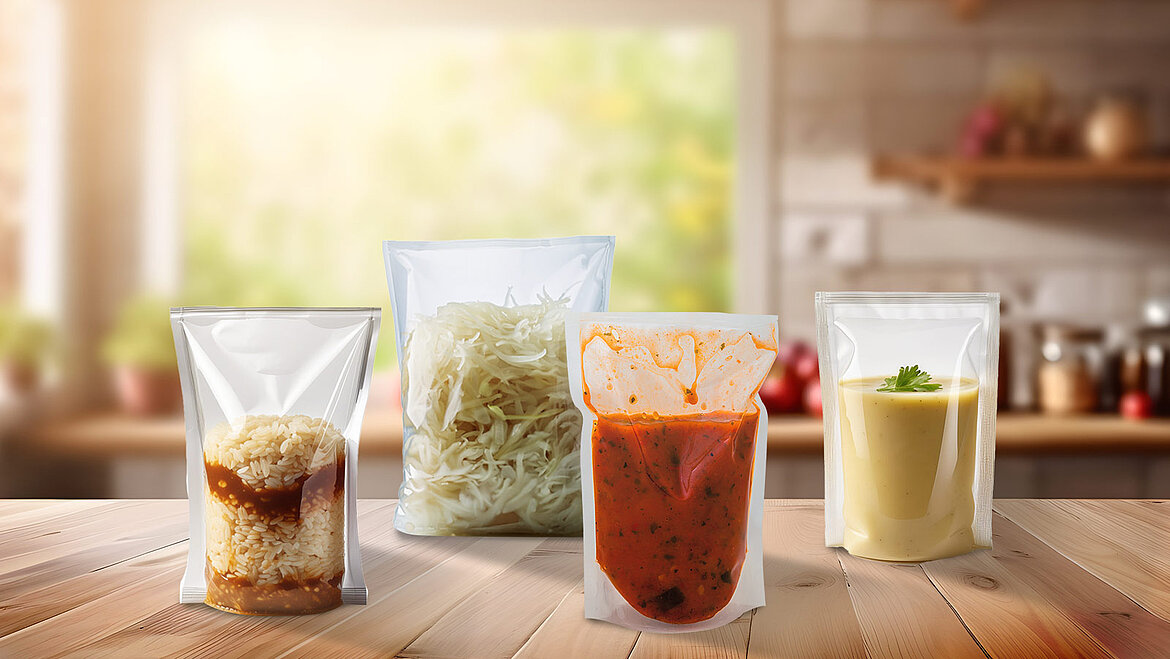
FAQ – The Most Important Questions and Answers about Sealing Food with Ultrasonics
Ultrasonic sealing is suitable for a wide range of packaging applications. The most common include:
- Stand-up pouches
- Chained bags
- Bags
- Cardboard packaging
- Spouts and valves
- Capsules and tea bags
- Switches, blister packs and trays
You can find an overview of the most frequently solved applications for ready meals here.
The high voltage created by the generator is converted into mechanical vibration (ultrasonics) in the converter. The welding tool (sonotrode) transfers this vibration to the film to be sealed. Frictional heat is generated, heating and melting the film inside within a very short time.
The mechanical vibration of the sonotrode causes the joining and simultaneous cooling of the seal, as the welding tools do not heat up. Therefore, ultrasonic sealing is also considered a cold welding process.
You can learn more about it here.
Ultrasonic sealing offers several advantages, including:
- Air-tight seals without additional joining agents or aluminum layers
- Hermetic seals even with contamination or product residue in the sealing area
- Lower material consumption thanks to particularly slim seals
- Up to 80 percent less energy consumption without heating or cooling the modules and packaging
- Fast process cycles of 100 to 200 milliseconds
- Precise controller enables reliable and repeatable seals with a near-perfect appearance, even with narrow process windows for sensitive materials
- Cold welding tools prevent burns to the material and thermal effects on the packaging contents
Ultrasonics can help you meet key requirements of the PPWR, including:
- Using recyclable materials:
Cold sealing tools and precise controllers allow safe sealing of sustainable materials such as mono-materials or paper-based materials. Our application experts can advise on switching to these sensitive materials.
- Reducing packaging size:
Ultrasonics reliably seals through contamination in the sealing area, allowing for a significantly smaller seal width compared to conventional technologies. This can save 5 to 10 millimeters per package, reducing packaging size, material consumption, and costs.
We would be happy to conduct initial feasibility trials with you in our ultrasonic laboratory and test your application. Simply make an appointment and contact us here.
Downloads Expert Resources
Learn more about the benefits of our technology for your food applications. Our downloads contain the knowledge from over 60 years of ultrasonics, providing valuable insights into advanced assembly techniques. By sharing our technical knowledge with you, we ensure a close partnership on equal terms so that we can realize projects as quickly and successfully as possible.
Download our exclusive resources to unlock decades of innovation and stay ahead in the rapidly evolving food industry.
Partner with Us
Contact our PACKAGING Team to discover how our premium solutions can elevate the quality and effectiveness of your large-scale manufacturing. We look forward to hearing from you!