Ultrasonic welding of plastics
Ultrasonic welding is especially suited to welding thermoplastic materials. During the ultrasonic welding of plastics, ultrasonic waves with frequencies of 15 – 70 kHz are used. With an amplitude of 5 – 50 μm, the oscillations are introduced into the component by the sonotrodes. Friction heat is generated and this leads to melting.
Under additional pressure, the plastics are then joined.To be able to weld precisely with ultrasonics, the energy from the sound waves must be focused.
This is achieved through the geometry of the tools (sonotrode and anvil) or the plastic itself (joint design). Points or edges on the seam can focus the energy. This is why they are known as energy directors (ED for short).
Advantages in the ultrasonic welding of plastics
The ultrasonic welding process offers a number of advantages. The most important of these are:
- Time savings: The plastics are welded in split seconds. There is no need for start-up and waiting times for the tools to heat up and cool down in the case of ultrasonic welding.
- Consistent quality: Precise control technology ensures precise and reproducible results.
- Cost-saving and environmentally friendly: No tools or other aids such as adhesives are required and less energy is used.
Joint design
The joint design has a particular influence on the form-fit joint connection. There are various joint geometries which are adapted to suit materials and components.
Die components are shaped like steps with energy directors. The ultrasonic waves cause melting at the energy directors and, under additional pressure, a tight, visually flawless and strong bond is created between the components.
- Simple creation of the joint
- "Tetris effect" (self-centering of the components)
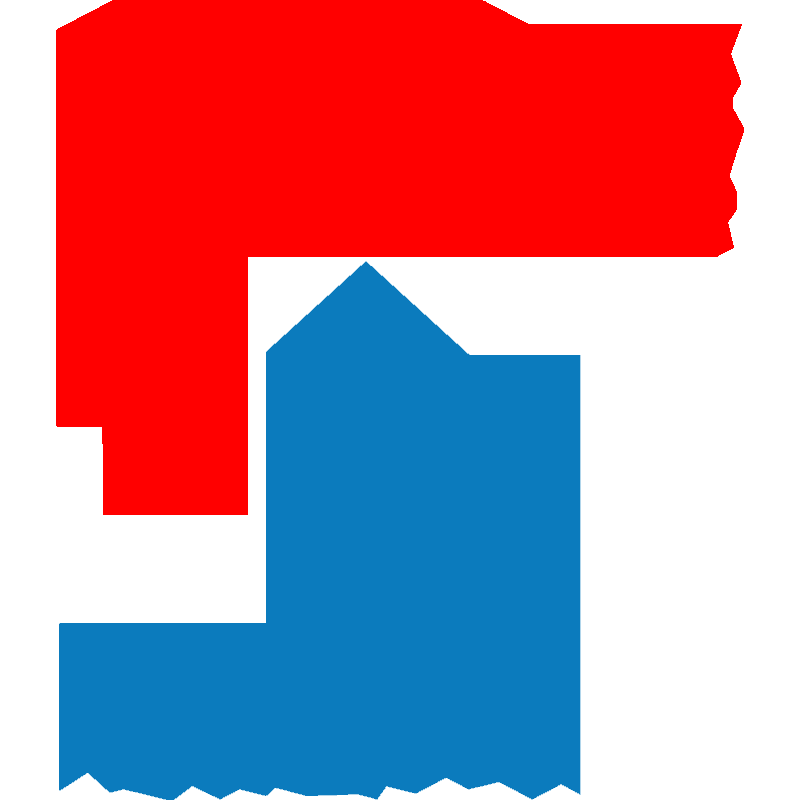
The bottom component has a gap (groove). The top component has a protrusion known as the “tongue,” which fits perfectly into the groove. The energy director of the tongue focuses the energy, melting occurs and, with additional pressure, the components are joined. It is essential that the groove have a large wall thickness.
- Greatest strength
- Precise connection
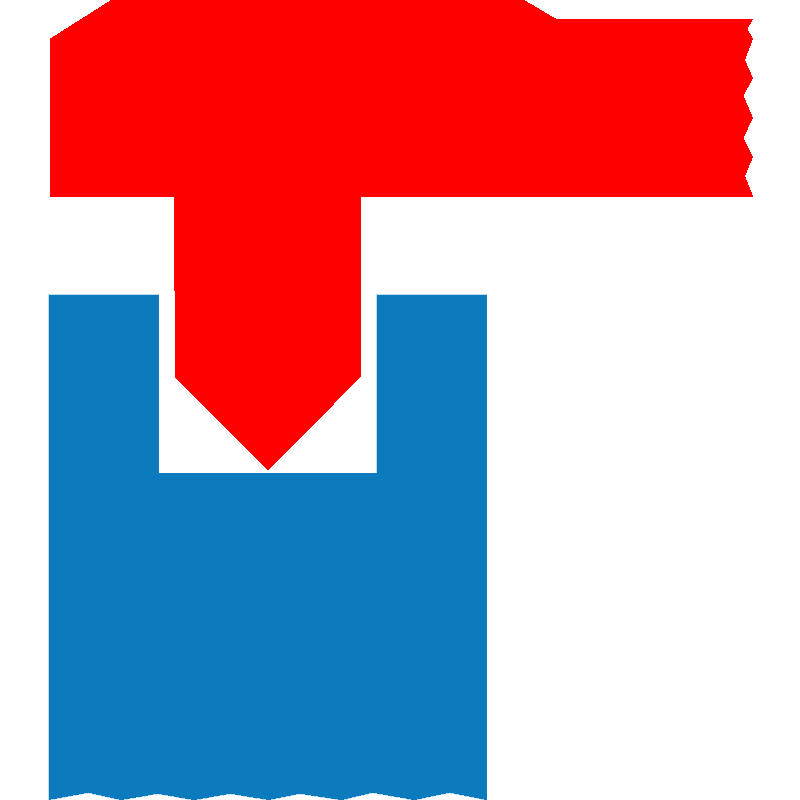
The melting process starts at the energy directors. Then, the top component is pushed down onto the vertical wall of the top plastic under controlled pressure. The heat that develops is what joins the two materials.
- Perfect joining of semi-crystalline plastics (the molecular chains in the materials have a regular arrangement)
- Tight and firm
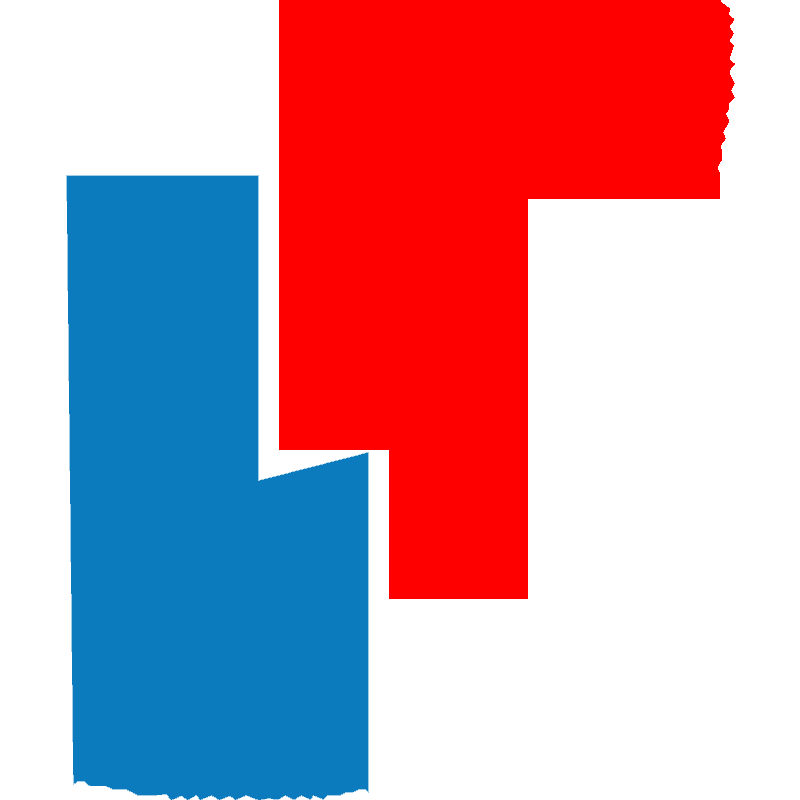
Plastics can be joined with metals or non-weldable materials via staking. The staking pins on the plastic are deformed so that they fix the material on top into place.
- Joining different types of materials
- No additional consumables required
- Quick and clean
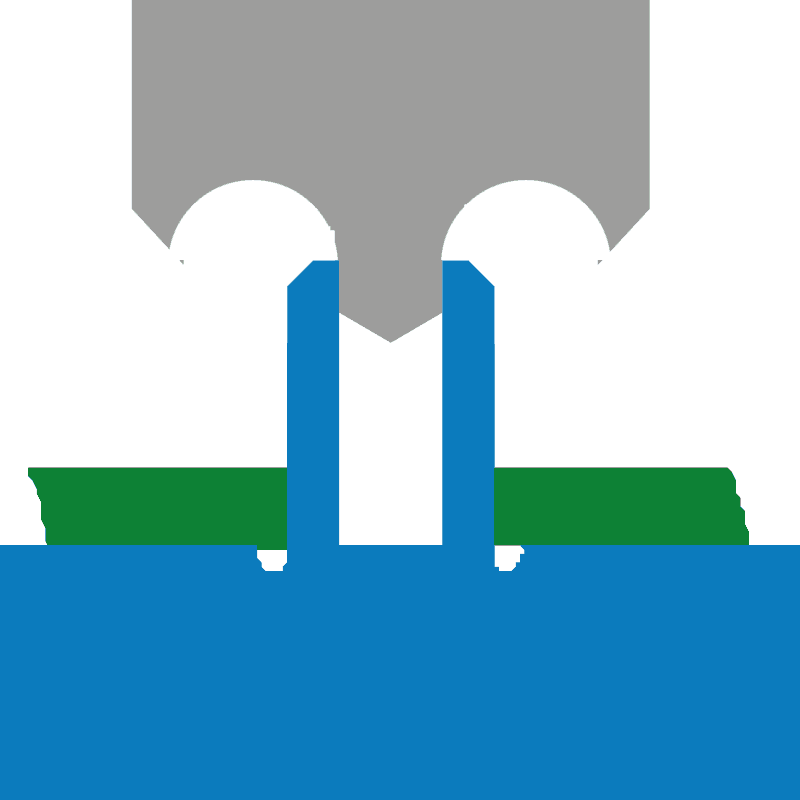
The bottom component has a notch where the walls converge to one point. The top component is positioned centrally. Ultrasonics and the additional pressure cause the energy director to melt and take on the shape of the notch. This is how both plastic can be joined.
- Joining components with thin walls
- Precise joint due to centering unit
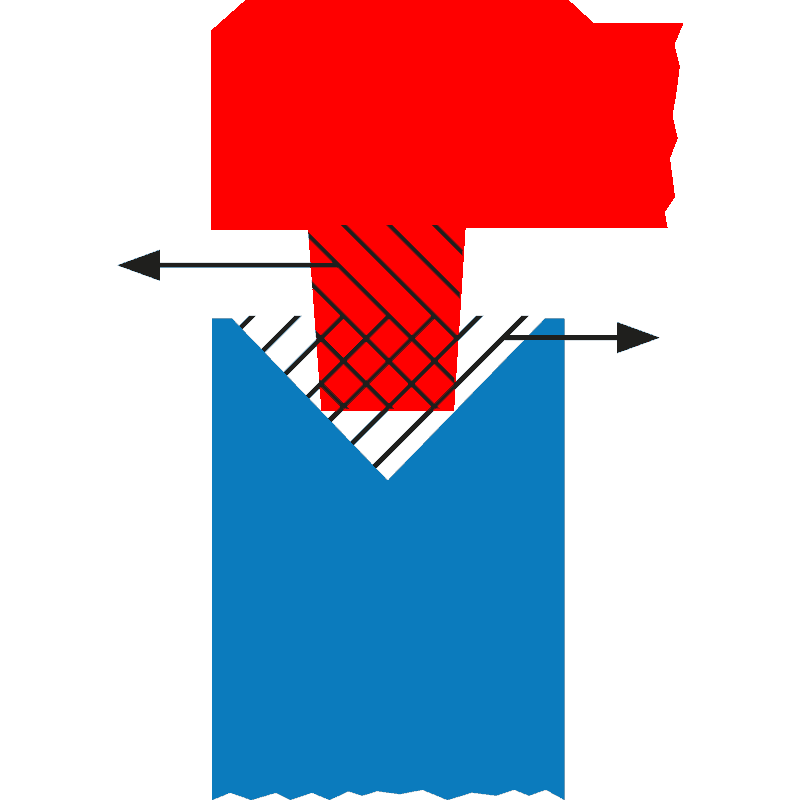
Used as an alternative to staking if the staking pins cannot be sprayed onto the component. This is why the sonotrode "springs" into action: Its front surface is specifically shaped and can reshape the plastic part so that the second material can be fixed into place.
- No energy directors required
- Joining different types of materials
- Large-scale reshaping possible
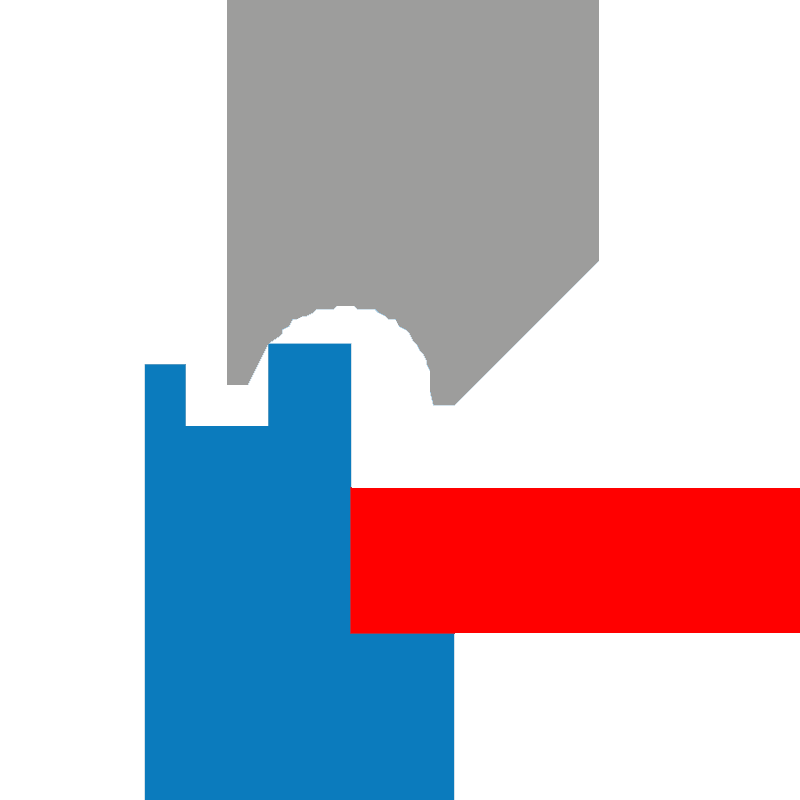
The components lie flat on top of each other without any special joint design. The tip of the sonotrode penetrates into the bottom plate. At this point, the plastic melts, partly collects in the joint and produces a local, spot weld.
- No energy directors required
- Precise joining
- Simple, quick and form-fit joint
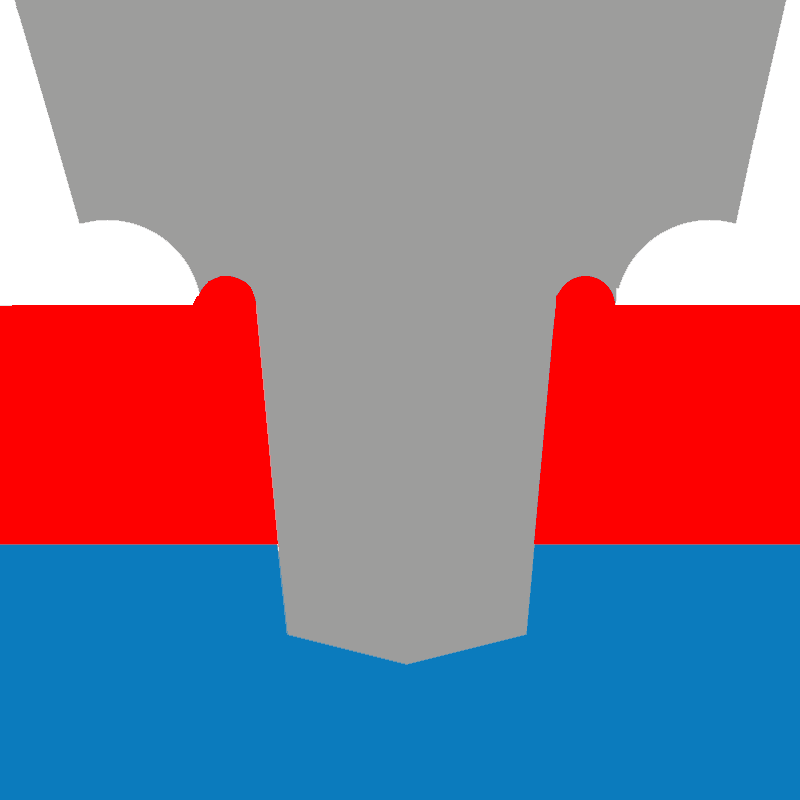