Automated Manufacturing of Hospital Care Devices with Ultrasonic Welding
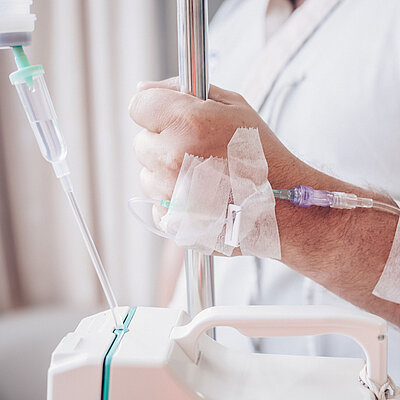
Produce faster and save costs at the same time: With ultrasonic welding, you can automatically produce catheters, connectors, or medical laboratory equipment in high volumes. Thanks to the digital, intelligent quality control and the efficient process, you can permanently optimize the costs and output of your production.
Benefits from our ultrasonic welding technology for your hospital care products:
- Minimal process cycles
- Automated, digital process control
- Clean Process without chemical bonding materials
Learn more about the benefits of ultrasonics for your medical product!
Discover Our Ultrasonic Welding Solutions For Your Medical Devices
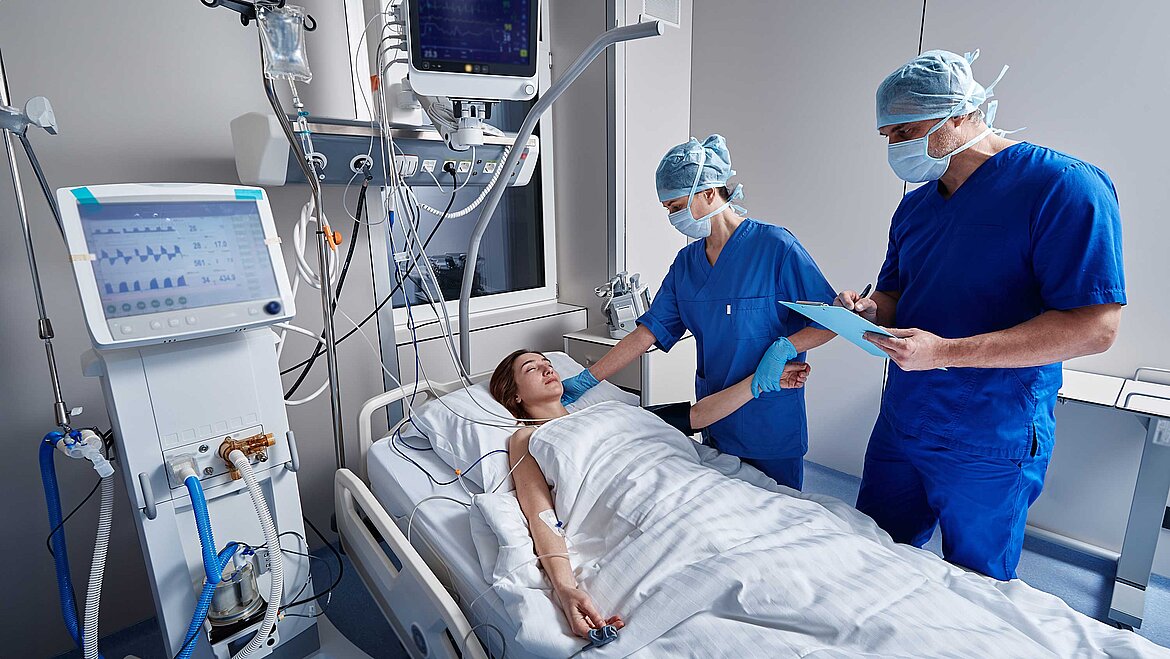
Didn't find your product?
White Paper: Automated and Safe Connections for Hospital Care Products
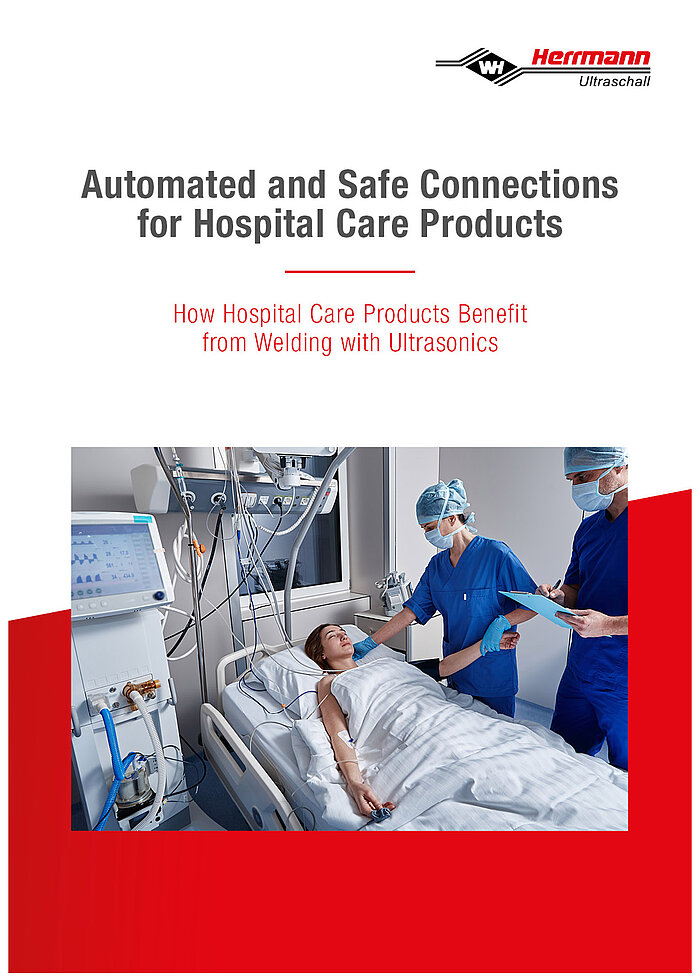
Faster, safer, more efficient: Optimize the manufacturing of your hospital care products with our ultrasonic technology!
In our free white paper, we'll show you:
- How ultrasonic welding increases the output of your manufacturing
- Common applications that can be successfully solved using ultrasonics
- Valuable insights: How ultrasonics welding works
OR
FAQ – The Most Important Questions and Answers about Welding with Ultrasonics
Ultrasonics can be used for the strong and permanent connection of all common thermoplastic materials, including PP, ABS, PC, etc., with minimal welding times of approx. 80 to 500 milliseconds. This makes the process ideal for manufacturing large quantities.
As no adhesives or other joining agents are required for the connections, there is no need for time-consuming cleaning work, heating up the tools or curing the adhesives, which speeds up the entire joining process.
Thanks to their compact design, ultrasonic welding systems can also be integrated into existing production systems and can precisely monitor even the fastest joining processes.
Find out more in our blog post on automated welding of medical products.
Known for its safety, precision and speed, ultrasonic welding is a widely used and reliable manufacturing process.
We achieve this by individually defining the right welding parameters for each application in our ultrasonic laboratory. These parameters are saved in the generator of your welding system and can be reliably reproduced for each individual welding process in your manufacturing.
The welding system's intelligent controller software ensures this exact reproduction. It monitors the process and measures up to 150 data records per weld. This not only makes the process safe, but also enables uncomplicated, digital quality control.
In ultrasonic welding, process capability (CpK) ensures that the welding process consistently produces parts within specification limits, while Overall Equipment Effectiveness (OEE) measures the machine's efficiency by evaluating availability, performance, and quality. A high CpK and OEE indicate that the ultrasonic welding process is optimized for minimal variation, high-quality welds, and maximum productivity.
This enables us to guarantee the flawless functioning of numerous applications in important areas such as infusion therapy, surgery and hemodialysis.
Learn more about the digital process control for medical product in our white paper.
Although ultrasonic welding is a mechanical joining process, it connects components extremely gently and is also perfect for joining smaller applications.
In addition to defining the right process parameters, two things are particularly crucial:
- The adjustment of the welding tools: the material and shape of our welding tools are individually adapted to the application. This ensures that the ultrasonic vibrations are introduced as gently as possible.
- The joint design: Components must have a special geometry at the contact points for welding with ultrasonics — we call this “joint design”. With the right design of the component, even the thinnest wall thicknesses can be safely connected. Thanks to their experience, our experts can consult you on exactly how such a joint design should look for your individual requirements.
You can find more information on connecting plastic parts with ultrasonics in our white paper “The biggest success factors in component design”.
From syringes and filters to surgical instruments: Ultrasonic welding is used in a wide range of applications — often multiple times within a single application.
The joining process is most frequently used in the field of hospital applications to:
- Welding of injection-molded parts
- Embedding of membranes, adhesive tapes, nonwoven materials etc.
- Swaging e.g. a silicone septum, a metal mesh etc.
- Staking of e.g. PCB, metal components etc.
Here is an overview of the medical products most frequently solved with ultrasonics.
With our Herrmann Engineering, we create customized welding solutions tailored to your specific needs. To achieve this, a project process involves five phases:
- Analysis: we want to precisely understand your needs and your requirements for the application. The first step is therefore an intensive exchange about the project and its scope.
- Trusted Advisor: We consult you on important questions such as the design of the components and the choice of materials. Together, we will find the right machine solution for you and carry out initial feasibility tests in our ultrasonic laboratories.
- Application Engineering: In further welding tests, we define the ideal parameters for the welding process to meet all requirements. We provide you with detailed reports on the laboratory results and recommendations for further steps.
- Perfect Product: After the laboratory tests, the results are validated in your production environment. We train your staff in the use of our machines and provide support with integration.
- Global Service: After start-up of the welding systems, we are at your side worldwide with our service team. In addition, we offer individual training, spare part deliveries, maintenance work and many other services to ensure that your manufacturing runs reliably.
Frequently solved Hospital Care applications
Downloads
Learn more about the benefits of our technology for your medical applications. Our downloads contain the knowledge from over 60 years of ultrasonics, providing valuable insights into advanced assembly techniques. By sharing our technical knowledge with you, we ensure a close partnership on equal terms so that we can realize projects as quickly and successfully as possible.
Download our exclusive resources to unlock decades of innovation and stay ahead in the rapidly evolving medical device industry.
Partner with Us
Contact our Medical Team to discover how our premium solutions can elevate the quality and effectiveness of your large-scale manufacturing of medical devices.