Joining Plastics of Medical Devices Without Adhesive
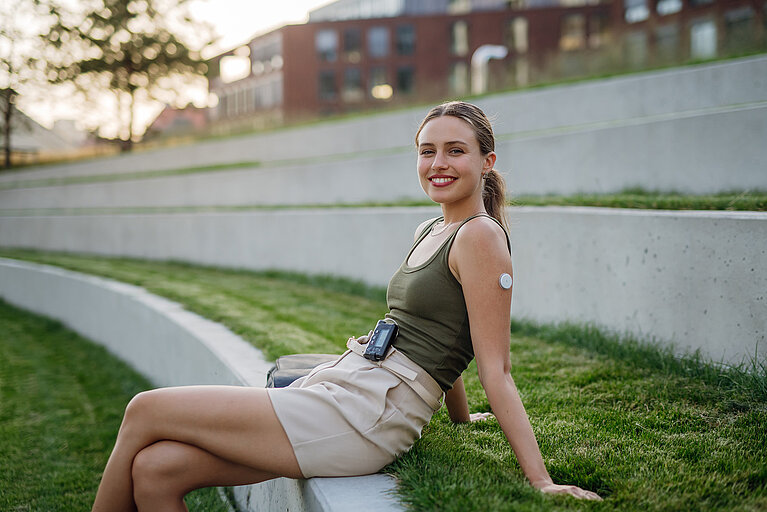
Creating Skin-friendly Connections with Ultrasonics
Particularly for medical products with direct skin contact, high wear comfort and skin compatibility are crucial for the quality of the product and customer satisfaction. Manufacturers should therefore avoid chemicals such as IBOA and connect plastics with processes that do not require adhesives, solvents or environmentally harmful substances - ultrasonics make this possible.
The use of wearable medical devices is increasing rapidly. With their high level of user-friendliness, they can permanently improve the quality of life of patients with diabetes or other illnesses. However, skin irritations can occur when using CGM sensors, insulin pumps or other wearables.
The most common cause: chemicals such as isobornyl acrylate (IBOA), which are found in adhesives. Studies show that up to 81 percent of patients who come into contact with them develop an allergic reactions, including severe irritation of the upper layer of the skin (contact dermatitis).
For products to be truly skin-friendly, plastics from wearables should be connected entirely without adhesives or similar joining agents. Read more to find out how.
Creating adhesive-free connections for plastics:
Ultrasonic welding is ideal for joining plastics permanently and safely without joining agents.
This is how it works: The welding system create mechanical vibrations that are transferred to the joining partners via the welding tool. Friction occurs in the joining zone defined beforehand. During the minimal process cycle of a few hundredths of a second - the plastic inside the component melts at these points, thanks to the strategic supply of energy. This creates a high-strength connection at the molecular level under minimal force and temperature.
Ultrasonic welding, staking, swaging and embedding have the greatest advantage since heating only occurs where it is really needed. This reduces thermal and mechanical stress in the component to a minimum, making ultrasonic welding suitable for sensitive components and products such as skin patches and sensors.
Using eco-friendly plastics:
Besides the joining process, the material must also be considered to make the application as skin-friendly as possible. More and more manufacturers are therefore switching from the commonly used polyvinyl chloride (PVC) to alternative thermoplastic materials.
PVC contains plasticizers that can have a negative impact on health. At the same time, this makes the plastic more difficult to dispose of, as it produces gases that are harmful to the environment and health when incinerated.
With ultrasonics, all common thermoplastic materials can be ideally connected. Tests in the ultrasonic laboratory are used to determine the right parameters to weld the plastic safely and consistently. The material itself is only subjected to minimal stress during the welding process and remains free of environmentally harmful substances. This preserves the original material properties.
As a result, the use of ultrasonics can significantly improve the environmental balance (product carbon footprint), the skin compatibility of medical wearables and patient satisfaction.
Discover how ultrasonic welding can help optimize the manufacture of your medical products.